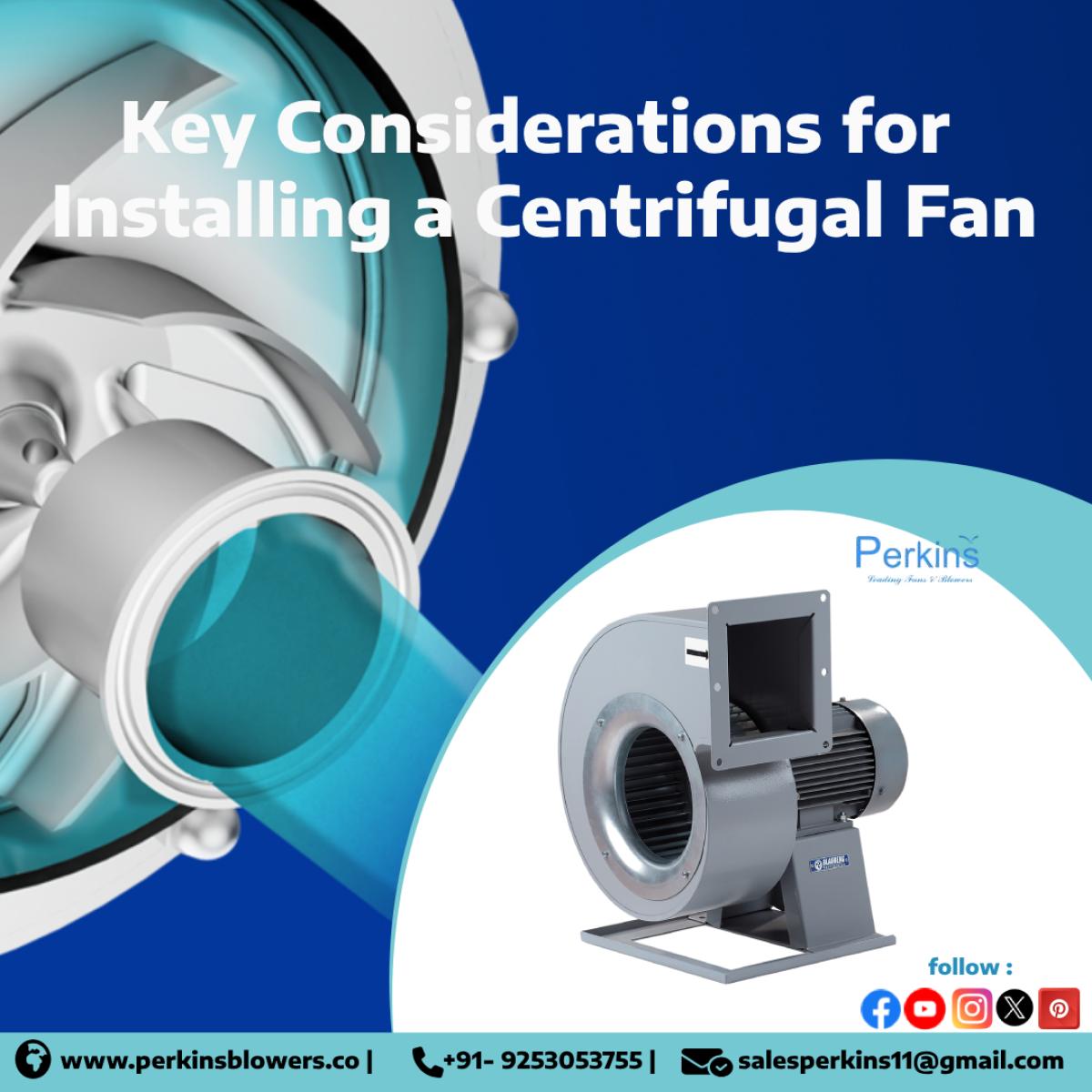
When it comes to industrial ventilation and air movement systems, centrifugal fans are a popular and reliable choice. Their robust design, ability to handle high pressures, and versatility across a wide range of applications make them essential components in factories, commercial buildings, and HVAC systems. However, installing a centrifugal fan is not as simple as just placing it in the desired location and switching it on. For efficient operation, optimal performance, and long-term reliability, several important factors must be considered during the installation process.
1. Purpose and Application
Before selecting and installing a centrifugal fan, it's crucial to define its intended purpose. Is the fan going to be used for general ventilation, dust collection, combustion air supply, fume extraction, or cooling? Different applications require different types of fans, with specific airflow capacities, pressure ratings, and material constructions. For instance, a fan used in a corrosive environment like a chemical plant may need to be made from stainless steel or coated materials to resist damage. Understanding the operational goals helps in choosing the right type of centrifugal fan and determining its proper installation parameters.
2. Airflow and Pressure Requirements
A key technical consideration is calculating the airflow (measured in CFM – cubic feet per minute) and static pressure requirements of the system. The performance of the centrifugal fan must match the demands of the ventilation or duct system to ensure proper air circulation. An undersized fan may fail to deliver the necessary airflow, leading to overheating or poor air quality, while an oversized fan can cause excessive energy consumption and noise. Proper sizing using fan curves and pressure drop calculations is a critical step prior to installation.
3. Fan Location and Mounting Surface
The location where the centrifugal fan is to be installed significantly affects its performance. The fan should be placed in a clean, accessible, and vibration-free area, away from dust, moisture, and corrosive elements. Adequate space around the fan should be ensured for maintenance and inspection. The mounting surface must be level and rigid to prevent misalignment and vibration during operation. Vibration isolation pads or flexible connections can be used to reduce structural vibrations and enhance performance.
4. Ductwork Design and Alignment
The efficiency of a centrifugal fan is highly influenced by the design and layout of the ducting system. Poor duct design, sharp bends, or misaligned connections can create turbulence and increase resistance, lowering the overall system efficiency. Inlet and outlet ducts should be properly aligned with the fan’s flanges to avoid airflow obstruction. Whenever possible, use gradual transitions rather than sudden expansions or contractions in duct size. Also, ensure that dampers or filters are installed at accessible points for easy maintenance.
5. Power Supply and Motor Compatibility
A centrifugal fan is typically powered by an electric motor, and it’s vital to ensure that the motor specifications match the electrical supply available at the installation site. Check voltage, frequency, and phase compatibility to avoid damage. The motor should be properly grounded, and all wiring must comply with local electrical standards. In the case of variable speed fans, a compatible VFD (Variable Frequency Drive) should be installed for speed control. Always ensure that motor protection devices like overload relays or thermal protection are in place.
6. Vibration and Noise Control
Centrifugal fans can generate noise and vibrations during operation, especially at high speeds. To minimize this, it’s recommended to use anti-vibration mounts, flexible duct connectors, and acoustic insulation where needed. Fans should be dynamically balanced before installation to prevent uneven load distribution. Regular monitoring of vibration levels post-installation can help in early detection of bearing wear or impeller imbalance.
7. Safety and Accessibility
Safety should never be compromised during fan installation. The fan should be installed in a way that prevents accidental contact with moving parts. Guards, protective grills, or enclosures may be necessary depending on the location. Ensure that emergency shutdown switches are easily accessible. Maintenance access is another vital factor—components like bearings, belts, and motors should be reachable without the need for major disassembly.
8. Environmental Considerations
Consider the ambient conditions where the fan will operate. High temperatures, humidity, chemical fumes, or explosive dusts require special fan designs, materials, and certifications. For instance, ATEX-certified fans are necessary in potentially explosive environments. Fans used outdoors may need weatherproof housings or rain hoods.
9. Compliance and Standards
Finally, ensure that the fan installation complies with local and international standards related to performance, safety, and environmental impact. Reputable centrifugal fan manufacturers like Perkins Blowers design their products in accordance with global benchmarks such as AMCA, ISO, and CE standards, ensuring reliability and efficiency.
Conclusion
Installing a centrifugal fan is a technical process that requires thorough planning, precision, and attention to detail. From selecting the right fan for your application to aligning ductwork and ensuring safe electrical connections, each step plays a critical role in achieving optimal performance. By considering the above factors, businesses can maximize the lifespan, efficiency, and reliability of their centrifugal fan systems. Partnering with experienced manufacturers like Perkins Blowers can further ease the process, offering expert guidance, high-quality equipment, and long-term support.