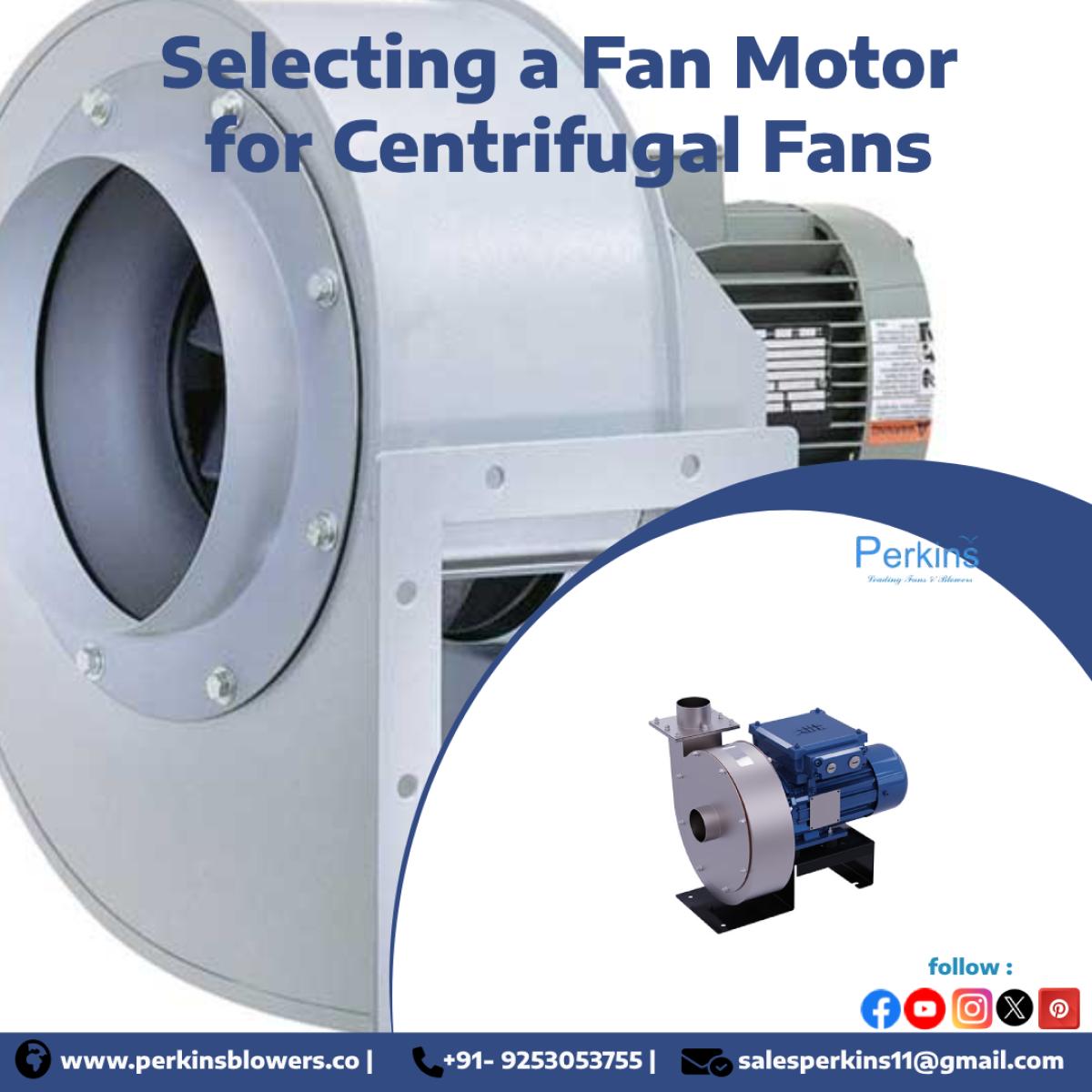
Selecting the right motor for a centrifugal fan is a crucial step in ensuring reliable, energy-efficient, and long-lasting operation. A fan motor is the driving force behind the entire air movement system, and its performance directly affects the fan's airflow, efficiency, and durability. Whether used in industrial ventilation, HVAC systems, manufacturing processes, or dust collection setups, a mismatched or poorly selected motor can result in energy losses, overheating, equipment failure, and costly downtime. To avoid these issues, several important factors should be taken into account when choosing a motor for centrifugal fans.
1. Power Requirements (Horsepower and Torque)
One of the most fundamental considerations is determining the required power output of the motor. This depends on the size of the fan, the volume of air it needs to move (CFM), and the static pressure resistance in the system. The motor must be capable of providing sufficient torque to start and operate the fan without overloading. Oversized motors lead to unnecessary energy consumption, while undersized ones may overheat or fail prematurely. Accurately calculating the brake horsepower (BHP) needed for the fan, with some margin for safety, ensures proper motor selection.
2. Speed (RPM) Compatibility
Centrifugal fans operate efficiently at specific speeds, which must align with the motor’s RPM (revolutions per minute). Direct-drive fans require motors that match the fan’s operational speed, while belt-driven fans offer more flexibility in speed adjustment. In applications where variable airflow is needed, using a variable speed motor with a compatible VFD (Variable Frequency Drive) allows for greater control and energy savings. Matching the motor speed with the fan’s design point ensures optimal performance and avoids issues like vibration or low airflow.
3. Voltage, Frequency, and Phase
The motor must be compatible with the available power supply at the installation site. This includes voltage rating (e.g., 230V, 415V), frequency (50 Hz or 60 Hz), and phase type (single-phase or three-phase). Most industrial centrifugal fans require three-phase motors due to their efficiency and ability to handle heavy loads. Selecting a motor that aligns with the electrical infrastructure helps prevent motor burnout, inefficiency, or malfunction. It’s also essential to verify the motor's insulation class and thermal ratings for safe and continuous operation under the given voltage and temperature conditions.
4. Motor Type: Induction vs. Synchronous vs. Brushless
The most commonly used motor for centrifugal fans is the squirrel cage induction motor due to its simplicity, ruggedness, and low maintenance. However, in some precision-controlled applications, synchronous motors or brushless DC motors may be preferable. Synchronous motors maintain constant speed under varying loads, while brushless motors offer higher efficiency and longer lifespan. The choice depends on the application’s specific requirements, including speed control, efficiency targets, and budget constraints.
5. Enclosure Type and Cooling Method
Depending on the installation environment, the motor's enclosure type becomes a critical consideration. For dusty or moist environments, a totally enclosed fan-cooled (TEFC) motor is ideal as it protects internal components from contaminants. In clean, indoor environments, an open drip-proof (ODP) motor may be sufficient. Hazardous locations may require explosion-proof enclosures. Additionally, the motor’s cooling method—whether fan-cooled, water-cooled, or self-ventilated—should be compatible with ambient conditions to prevent overheating and ensure consistent operation.
6. Efficiency and Energy Consumption
With increasing focus on energy conservation and sustainability, choosing a high-efficiency motor is more important than ever. Premium efficiency motors (IE3 or IE4 classified) may have a higher initial cost but offer significant long-term savings in energy bills and reduced carbon footprint. In many countries, energy efficiency regulations mandate the use of motors that meet minimum efficiency standards. When selecting a motor for a centrifugal fan, it’s advisable to compare energy ratings and life-cycle costs alongside upfront expenses.
7. Load Type and Duty Cycle
Centrifugal fans generally impose a variable torque load on the motor, meaning the torque increases with speed. Motors selected must be capable of handling this load profile without frequent overheating. Additionally, understanding the duty cycle—whether the fan operates continuously, intermittently, or under fluctuating loads—helps in choosing a motor that can endure the required level of operation without failure. Motors designed for continuous duty (Class S1) are typically preferred for industrial fans that run non-stop.
8. Environmental and Ambient Conditions
The operating environment significantly influences motor performance and longevity. Factors such as ambient temperature, humidity, altitude, dust, chemical exposure, and vibration levels should all be taken into account. Motors installed in high-temperature areas need to have suitable thermal protection and higher insulation classes. For outdoor or corrosive environments, motors with special coatings or sealed enclosures are essential. A detailed understanding of environmental conditions helps in selecting a motor that remains reliable under real-world challenges.
9. Maintenance and Serviceability
Ease of maintenance and availability of spare parts should also be considered during motor selection. Motors that come with readily replaceable bearings, accessible terminals, and standard frame sizes simplify repairs and reduce downtime. Choosing motors from reputed manufacturers with good service support and warranty coverage, like those used in Perkins Blowers centrifugal fan systems, ensures long-term reliability and peace of mind.
10. Integration with Control Systems
Finally, the motor should be compatible with any control or automation systems in use. Modern industrial setups often integrate motors with sensors, VFDs, or building management systems (BMS) for remote monitoring and intelligent control. Motors that support digital communication protocols (like Modbu
Conclusion
Selecting the right motor for a centrifugal fan goes beyond just matching power and speed ratings. It requires a holistic evaluation of operational needs, environmental conditions, efficiency goals, and control requirements. Each factor plays a crucial role in determining the fan system’s reliability, performance, and cost-effectiveness. By carefully assessing these elements, industries can make informed decisions that enhance productivity and minimize operational risks. Trusted centrifugal fan manufacturers like Perkins Blowers provide not only high-quality fans but also expert guidance in motor selection, helping clients achieve the best results from their ventilation systems.
Read more: Key Considerations for Installing a Centrifugal Fan